Reliable manufacturing scale-up for Fortescue Zero
Agile ways of working to meet timescales and quality, exceeding customer expectations.
The programme
Battery system development, production and testing for an autonomous vehicle application.
Hyperbat supported DFMEA and led the development of the PFMEA and control plans to ensure production processes were reliable, robust and repeatable to an automotive standard.
The team designed, installed and commissioned the production line to manufacture 7 prototype packs a week, up to 70 modules a week, 576 cylindrical cells per module. This included the development of automated processes and full end of line test capability.
Hyperbat value add
Exceeding customer expectations
Agile and ways of working to manage design developments whilst meeting all cost, quality and delivery requirements for the DVP prototype build phases.
Quality embedded
Full traceability and digital conformance of no-fault-forward controls and monitoring data for every battery component.
In-house testing
Module and end-of-line functional performance testing within our in-house Battery Testing Facility.
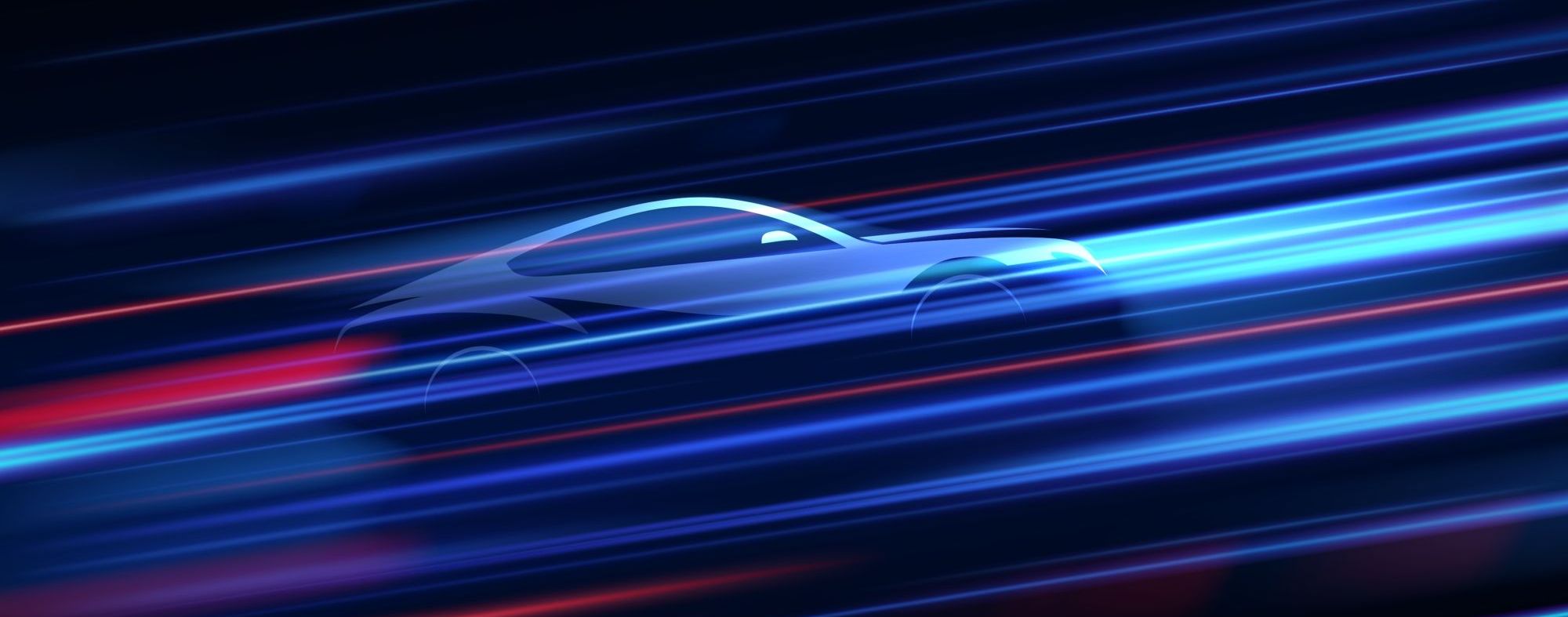
Browse case studies

Build-to-print manufacturing for the Lotus Evija
Flexible production rate based on customer pull & managing complex supply chain. Find out more
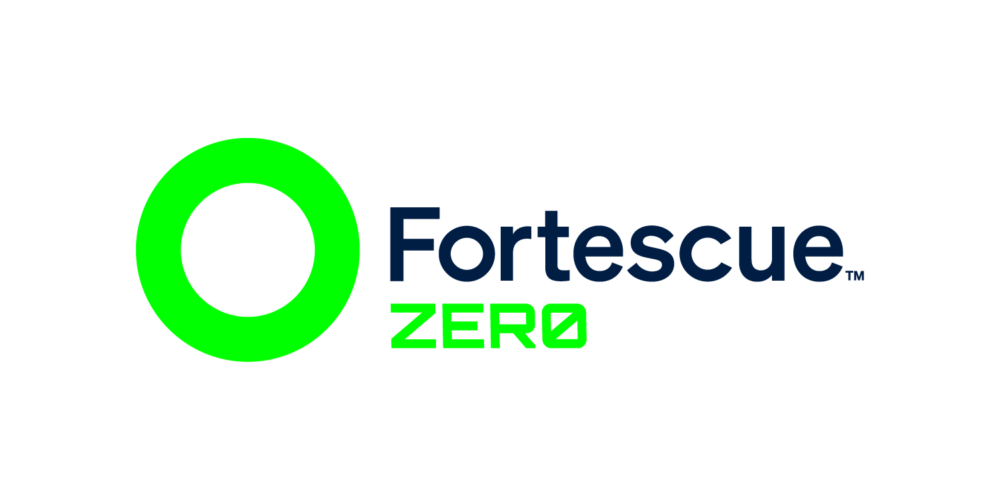
Reliable manufacturing scale-up for Fortescue Zero
Agile ways of working to meet timescales and quality, exceeding customer expectations. Find out more
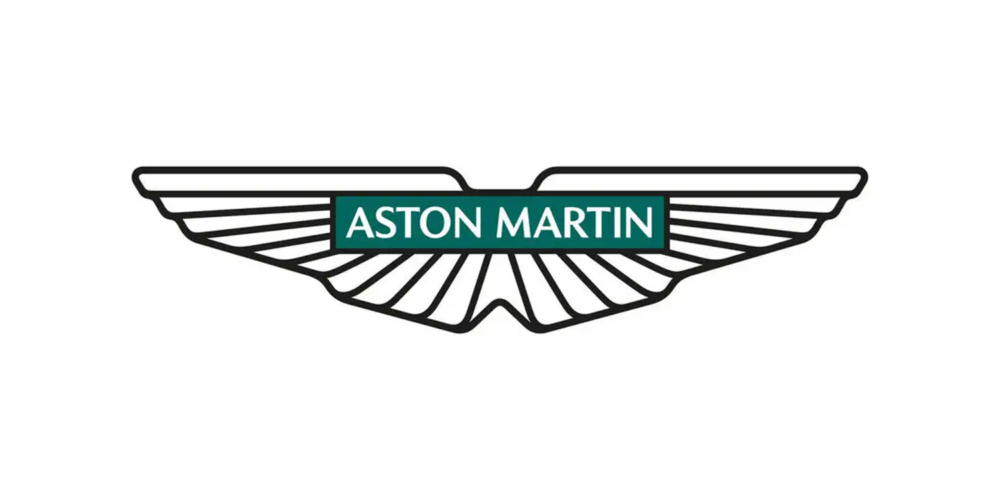
Battery system development of the Aston Martin Rapide E
APC funded project to develop a UK battery supply chain & establish Hyperbat capability. Find out more